WEINIG finger jointing lines: The fastest way to create higher value
Finger jointing is recognized as the most stable method of wood length joints. And if you require this technology, there's no better exponent than WEINIG. We are the specialists and have been number 1 on the market for over 25 years. WEINIG finger jointing technology is focused on maximum precision. This means minimal dimensional allowance, wood losses and operating costs. All systems are extremely user-friendly. This makes residual wood processing and upgrading by finger jointing profitable and easy for you!
The flexible modular design allows machines to be equipped according to your individual requirements. This enables high flexibility for standardized as well as customer-specific solutions, regardless of whether the systems have raw wood entry lengths, smaller or larger than 1,000 mm. The principle can be used for all performance classes: From the SOLID JOINT PS 2000 entry model to the Ultra, CombiPact and Turbo-S models up to the high-performance class with the HS120 and HS200 horizontal finger jointing lines. In short: WEINIG system concepts are designed to meet the highest demands in quality for all performance classes.
WEINIG Short timber finger jointing lines
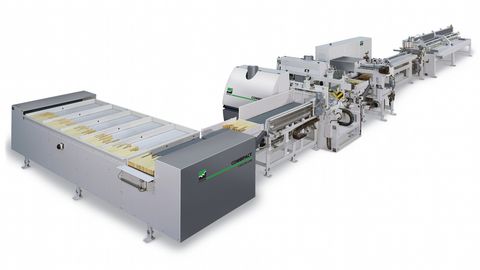
Feed speed from 6 m/min up to 70 m/min
- Finger joint profiles for all areas of use
- Maximum precision and stability of finger joints
- Robust and powerful
- High operational capacity, up to 200 pieces/min (28 km/8h-shiftr)
- Convenient and user-friendly
WEINIG Constructional timber lines
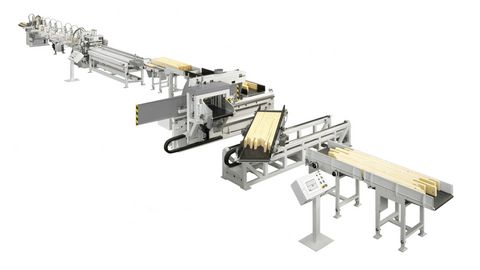
Feed speed up to 120 m/min
- Vertical and horizontal jointing is possible
- Long wood entry length such as 2 m, 3 m, 4 m or even 6 m
- Shaper heights (timber width) up to 300 mm
- Almost all glue types possible
- Front-end, extrusion, cycle or through-feed presses possible
WEINIG Compact finger jointing lines
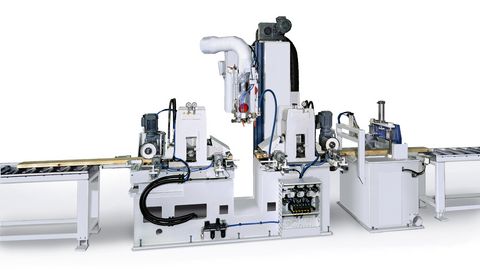
Feed speeds up to 70 m/min
- Very compact construction of different lines
- Pressing force of 20, 30 or even 40 tonnes
- Capacities of 3.5 up to 15 joints/min possible
- Optionally available with additional sound insulation cabinet
- Production of an endless phase
WEINIG Single board lines
Feed speed up to 160 (200) m/min
- Every work piece is individually aligned and processed.
- High-performance lines for capacities up to 160 (200) m/min.
- With automatic feeding system and stacking solutions
WEINIG Through-feed press
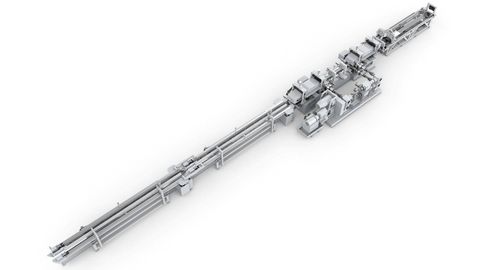
Feed speed up to 160 (200) m/min
- Pressing without stopping
- Cutting (sawing) without stopping
- All offset joints are realigned
- Can be combined with all high-performance finger joint shapers
- Direct planing after the press is possible