WEINIG Through-feed press: No offsetting in the presses at high speed
Using the through-feed press DKK, the feed-in line EUB and the following edging saw your can press all glued-wood products into a perfect strand and, if needed, cut them to fixed end lengths with the following edging saw.
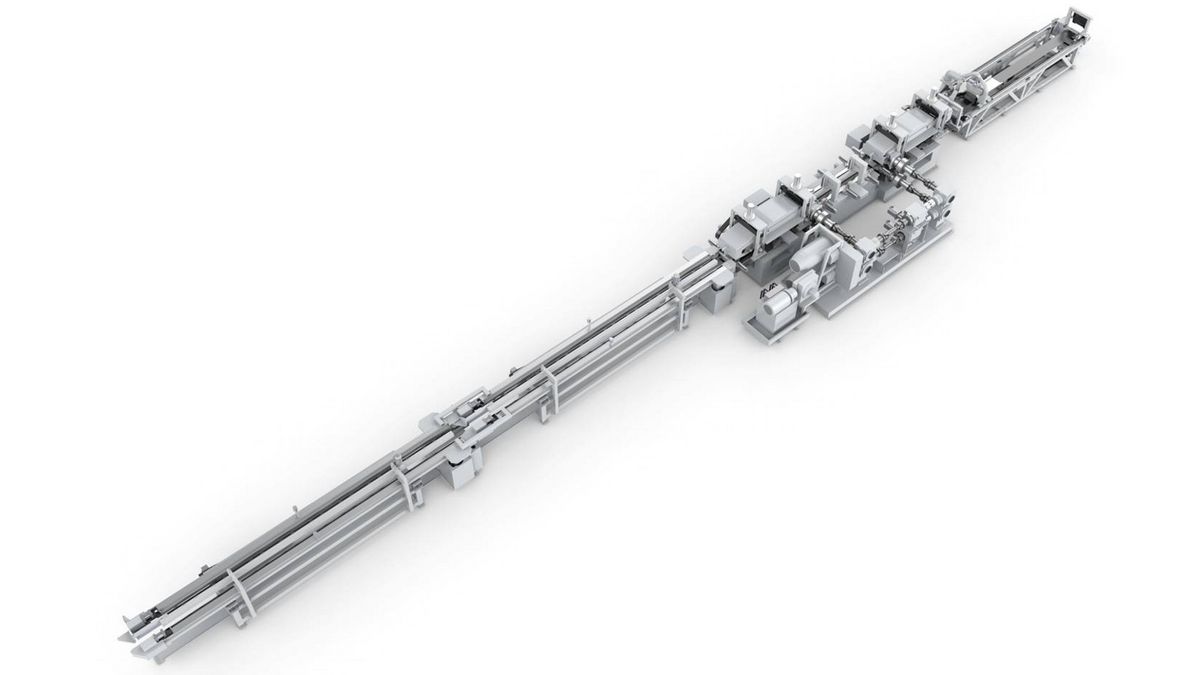
All machines
WEINIG Through-feed press
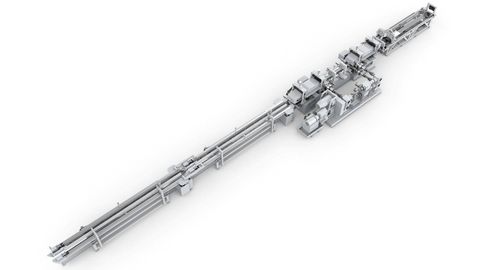
Your press for almost all glued-wood construction products.
- High quality of the end product by processing from all sides
- The through-feed press enables pressing without offsetting.
- Hardened plate chain for high durability
- Pressing in the throughfeed, without stopping
- Automatic cross sectional changing
The WEINIG through-feed press offers you
- Pressing without stopping
- Cutting (sawing) without stopping
- All offset joints are realigned
- Can be combined with all high-performance finger joint shapers
- Direct planing after the press is possible