WEINIG optimizing cross-cut saws: Pure performance and efficiency for the most advanced lengthwise cross-cutting
Cross-cutting –a simple process with more benefits than you might think - increased productivity, value creation, protection of resources and, not least, profit. Ultimately, every work piece must be cross-cut at some point during production. With SOLID CUT, you can automate and optimize your length cutting, guaranteeing you a reliably high daily output and production quality.
“Optimizing cross-cut saws are built for fast and precise cross-cutting of single boards in solid wood, panels and similar materials. Regardless of the type of cutting, the SOLID CUT series are not only the fastest but also the most reliable in their performance class. Every production run has its own different requirements and options. The modular design of the SOLID CUT series enables us to tailor your saw precisely to your wishes and requirements. Starting with the SOLID CUT TF 1500 as a single machine up to the fully automatic interlinked cutting system with up to four individual saws from the SOLID CUT TF 5000 series, we can offer you the right solution for your needs – all from a single source.
Our close contact with you "our customers" and focus on our core skill of "cross-cutting" has made us the technology leader. The high quality and availability of our machines in day-to-day production make "SOLID CUT" saws synonymous with length-optimized cross-cutting. This is evidenced by our "SOLID CUT TF 8000 Dimter Line – the fastest saws in the world"
WEINIG SOLID CUT TF 1500
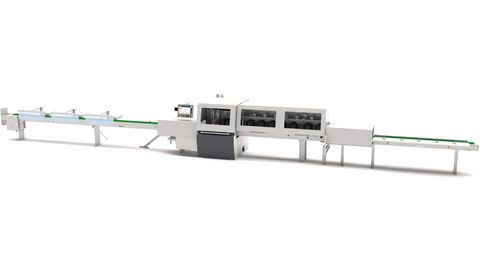
Built for automatic cross-cutting - come what may.
Detail page SOLID CUT TF 1500WEINIG SOLID CUT TF 2000 series
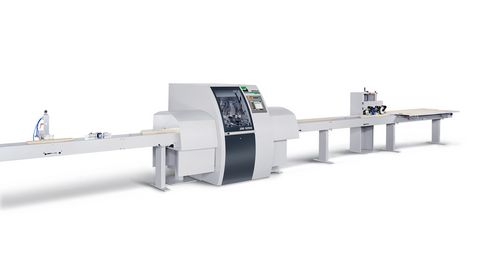
Strong concept for profitable, high-performance cross-cutting
Detail page SOLID CUT TF 2000 seriesWEINIG SOLID CUT TF 5000 series
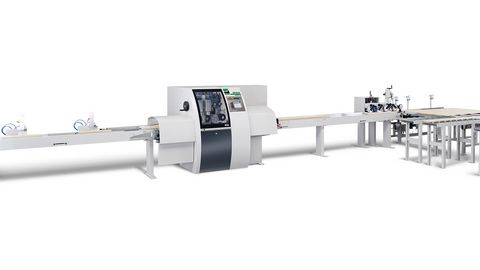